5 Costly ISO 9001 Mistakes – and How to Avoid Them
29 March 2025
ISO 9001 is the world's most popular quality management standard, with more than a million certified companies worldwide. But many companies make mistakes during the implementation phase, some of which impact on resources with potentially serious outcomes. In this article we shed light on the most severe ISO 9001 mistakes and show you not only how to avoid ISO 9001 nonconformities, but also costs and inefficiencies.
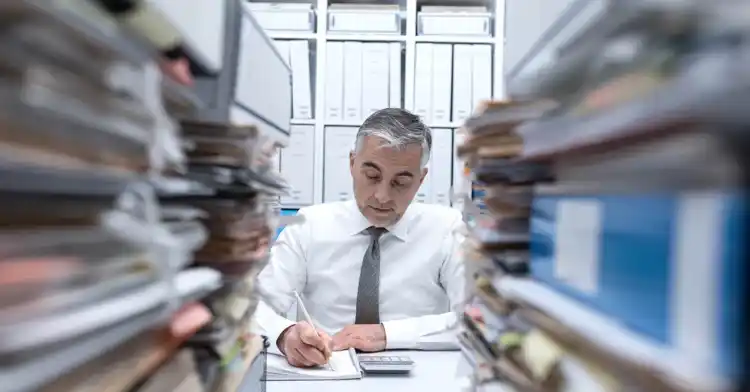
1. Costly ISO 9001 Mistake and How to Avoid ItSeeking ISO 9001 Certification for the Wrong Reasons
The most important benefits of ISO 9001 are usually operational rather than marketing related. In fact, ISO 9001 was designed as a tool for companies to improve their operations and bottom line; certifications and marketing benefits came later. Nevertheless, one of the most common ISO 9001 certification mistakes businesses make is their focus on marketing benefits. Companies that implement ISO 9001 mainly because of external pressure are unlikely to get the same, long-term benefits as organizations that seek better customer satisfaction, higher productivity and efficiency.
The Pitfall of Viewing ISO 9001 Certification Purely as a Marketing Tool
Consumers generally believe that products and services associated with ISO 9001 are of higher quality, so it stands to reason that advertising your certification provides a credibility boost. However, implementing a quality management system (QMS) solely for marketing purposes downplays other, more important benefits. No amount of marketing will ensure the success of your business if you're not focusing on ISO 9001 processes that produce quality goods and great customer satisfaction.
Defining the right reasons for seeking ISO 9001 certification is one of the first things you can do to increase the likelihood your quality management system will be a success.
The Danger of Pursuing Certification Solely Due to External Pressure
An increasing number of businesses, government departments and non-profit organizations require their suppliers to achieve ISO certification before they purchase their products and services. Government-Wide Acquisition Contracts (GWACs), as, for example, the NASA SEWP, are prime examples of sought-after opportunities that typically require ISO 9001 certification. But getting certified just because it's mandatory to access particular markets could backfire if the implementation process devolves into a quest for superficial compliance rather than an opportunity to improve operations. If your QMS fails and you can't deliver on your contractual obligations, not only will your customers be dissatisfied, there may be severe penalties and consequences.
The Risk of Implementing ISO 9001 Based on Competitor Actions Alone
If your competitors are ISO 9001 certified, you may feel you need to catch up. However, it's not enough if your actual products and services aren't as good or better than your competition. As stated already, a focus on certification simply for the sake of it won't lead to a QMS capable of reaping long-term benefits such as better quality, greater efficiency and lower costs.
How To Avoid Implementing ISO 9001 For The Wrong Reasons
While it might be quicker and cheaper to implement a QMS for the reasons discussed above, the maintenance and opportunity costs will be higher long term. In a nutshell, these quick and simple approaches are less likely to result in real, sustainable improvements in business operations and customer satisfaction.
Once you understand the requirements of the ISO 9001 standard and how they apply to your business, you will have a broad idea of the gaps in the way your organization operates. What do your customers, employees and managers have problems with or complain about, and how could implementing aspects of the standard make a positive difference? Documenting a pathway to success, and communicating that journey to your staff, increases the chances of realizing your objectives and reaping the rewards of highly functional QMS.
Read on to learn more about the costly mistakes that organizations make when implementing ISO 9001.
2. Costly ISO 9001 Mistake and How to Avoid ItLack of Support from Top Management
The second ISO 9001 pitfall is not having support from top managers for the implementation process. In small businesses, top management might refer to the company owner; in larger organizations the term refers to the executive and board of directors. If top management doesn't provide the leadership, resources and direction required, the likelihood of gaining certification and reaping the potential benefits is diminished.
Employees need authorization and empowerment from leaders to engage in improvement and change operational processes. If leaders don't buy into the system, they become the bottleneck rather than the enablers.
Risk and Consequences of Inadequate Top Management Commitment to ISO 9001
There are several sections in the ISO standard that spell out the expectations of top management for successful certification. While it's possible to delegate operational aspects of the QMS and empower employees to manage their part of the organization, the overall responsibility for the quality management system lies at the top.
The ISO standard requires that top management shows demonstrated commitment to the organization's quality management system. This means taking accountability for the QMS and communicating the importance of its requirements, requiring other managers to demonstrate their support for the system, and engaging, directing and supporting employees to make sure the system is effective.
How to Secure and Maintain Top Management Support for ISO 9001 Implementation
Leadership's visible use of the ISO 9001 system not only helps to avoid audit nonconformities but is crucial for the long-term success of your quality management system. Leadership that doesn't buy into ISO 9001 and refuses to "walk the talk" not only hinders the organization's path to certification, but discourages staff from maximizing the benefits of the ISO system. In addition, if top management doesn't fully support ISO 9001, required changes can often not be implemented.
In our experience, one of the easiest and most effective ways to ensure top management support is to provide vigorous training. We offer two training solutions to address this need, each with a proven track record of success:
With correct training, top management will fully understand the benefits that ISO 9001 brings, and will provide the necessary leadership. And once this support is communicated throughout the organization, the entire workforce is more likely to get involved and take ownership.
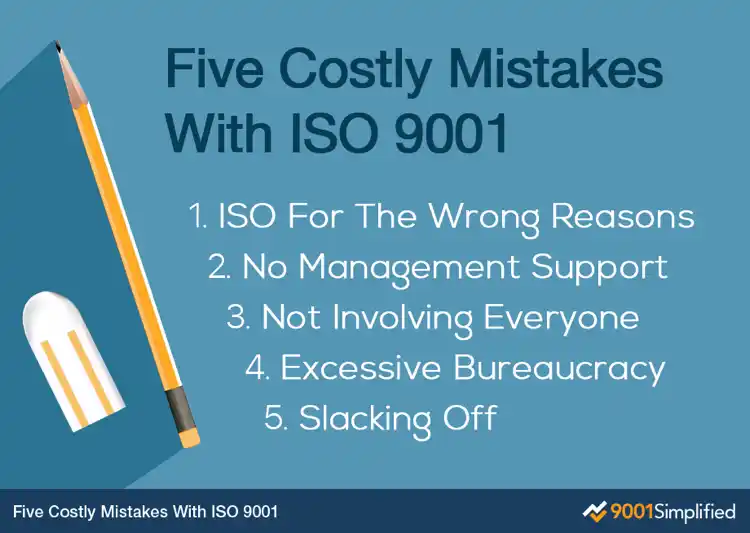
3. Costly ISO 9001 Mistake and How to Avoid ItEmployee Disengagement in ISO 9001 Implementation
As made clear in the previous sections, an organization's quality management system impacts on virtually all business processes, along with the roles and responsibilities of all employees. This is why it's essential that all staff are fully involved in the ISO implementation process, and why they must continue to support the QMS once certification has been achieved.
The Consequences of Insufficient Employee Involvement in ISO 9001
If employees aren't involved in the implementation process or don't understand their new responsibilities, they are likely to feel threatened and resentful. New responsibilities with no perceived benefit will lead to superficial compliance at best, or resistance to required changes at worst. Inertia and a lack of constructive input will impact on the success of the certification process, and the resulting QMS is unlikely to reflect the best way of doing things.
In addition, not involving everyone is a waste of valuable resources. Rank and file employees are usually well aware of problems with the way things are done and often have suggestions on how to improve them. However, they might not feel empowered to make these suggestions if they don't understand how their outputs contribute to the final product or service.
How to Achieve Employee Engagement in ISO 9001 Implementation
Education is great for ensuring that employees get involved. Proper training will show them the merits of the new ISO system, improve the way things are done and benefit them as individuals, along with the business itself. Initial training for everyone should focus on an introduction to ISO 9001:2015 certification and how the different aspects might apply to them. You can deliver training in small groups, at team meetings or one-on-one with key individuals.
Online courses are the most flexible way to provide cost-effective training with excellent outcomes. Employees can learn according to their own schedule, anytime and anywhere, with minimal impact on operations. A good online course, such as our ISO 9001:2015 Employee Training, creates buy-in and enthusiasm for ISO 9001 and encourages participation.
During the implementation process, give employees the chance to contribute to the changes and documentation that affect their jobs, and provide opportunities for them to get involved with the broader aspects of the QMS. Celebrate achievements regularly across the whole organization. Publicly recognize employees who actively engage and improve the way things are done. And when certification is successful, acknowledge that it's been a team effort.
4. Costly ISO 9001 Mistake and How to Avoid ItExcessive Bureaucracy
Excessively bureaucratic ISO systems must be avoided at all costs. Not only do they hinder operational performance, they sap motivation, involvement and support. More seriously, they cast doubts on the validity of the organization's QMS and the all-important benefits of ISO 9001.
If documents aren't necessary to support the operation of the business or improve the way things are done, then reassess their usefulness and either revise or discard them.
The Detrimental Impact of Superfluous ISO 9001 Documentation
In the early years of ISO 9001, excessively bureaucratic quality management systems were the norm. Few people really understood the ISO standard, and it was common for organizations and consultants to churn out ridiculous amounts of documentation. In fact, the top errors in ISO 9001 documentation have always been over-documentation without practical value for the user. Sure, the organizations got certified, but the resulting bureaucracy made the QMS a nightmare to manage and gave rise to the myth that ISO 9001 systems are a hindrance rather than a help.
These days things have somewhat changed and streamlined systems are more common, but overly documenting their processes and creating systems that are too complex and difficult to maintain remain the most common ISO 9001 certification mistakes small businesses make.
How to Streamline Your ISO 9001 Documentation
If you can honestly say you don't need any procedures, work instructions, forms or checklists to support your QMS, then perhaps you don't need to document anything. But it's worth noting that while you don't need procedures and work instructions, you still need to keep records to show that you meet the requirements of your QMS. The key to not creating too many documents is to evaluate the need for each one by asking questions like:
Is it relevant?
Is it useful for the people who need to do the job?
Are there other regulatory requirements that mandate it?
If documents aren't necessary to support the operation of the business or improve the way things are done, either revise or discard them. For example, the most recent revision of ISO 9001 no longer requires a Quality Manual. On the other hand, many external auditors still expect one, and a Quality Manual can be used as a handy marketing tool to show to clients prior to achieving certification. But if you see no merit in having one, then don't.
Consider too the best format for each document. A work instruction need not be long and wordy, and a simple flowchart, checklist, diagram or video might be more suitable.
Finally, take a look at our ISO 9001 documentation templates. These are designed not only to simplify your ISO 9001 implementation, but to ensure a lean and mean QMS that's free of bureaucracy and easy to manage. If you need further assistance, we provide free consulting and advice to make sure you stay on track.
5. Costly ISO 9001 Mistake and How to Avoid ItPost-Certification Complacency
Certification to ISO 9001 is cause for celebration. The business can use the ISO certificate, communicate the accomplishment in their marketing materials and compete for new contracts.
After all the effort that may have taken several months, it's now very easy to relax and ease off a bit. The audit program can slip behind, documents can quickly become out of date, training records lapse, and communication with employees about implementation progress becomes less frequent or ceases. Resources might be cut or reallocated to new programs. And before you know it, the QMS is no longer functioning the way it was designed.
Organizations must continually adapt to the external environment to survive. When they change the way they do things, the related elements of the Quality Management System should also improve.
The Risk of Complacency after ISO 9001 Certification
Slacking off after achieving ISO 9001 certification is a common ISO 9001 certification mistakes businesses make. However, initial certification to ISO 9001 is only the beginning: the quality management system requires effort to sustain and improve.
In addition, the original certificate is only ever valid for three years. External auditors will generally return at least once per year to conduct a surveillance audit and every three years for another full audit. When they return, the auditors expect to see evidence that the QMS is central to the way the organization runs its business and that processes are continuously improving. To satisfy the auditors, avoid ISO 9001 nonconformities, and maximize the rewards that the standard brings, there needs to be an ongoing effort by everyone to use, maintain and improve the quality management system.
How to Ensure Ongoing ISO 9001 Compliance
There are many things organizations can do to maintain momentum after getting certified. Firstly, celebrate the achievement with the whole organization. Emphasize all the goals and benefits that have been realized, and stress the rewards that ISO 9001 brings. Highlight the concept of continuous improvement, and make it clear to everyone that your QMS is a living entity that needs constant nurturing. And at all times, top management needs to continue to show support for the QMS and resource it appropriately.